In a 3-phase separator at a crude oil production facility, operators started to notice that there were frequent overshoots in the level reading.
In addition, as the gas is sent to a compression system, it was noticed that the downstream compressor suction scrubber started to receive more liquids than usual. Remember that the compressor suction separator is not expected to receive liquids but it is usually added as a safeguard to the compressor. So now it is starting to receive liquids.
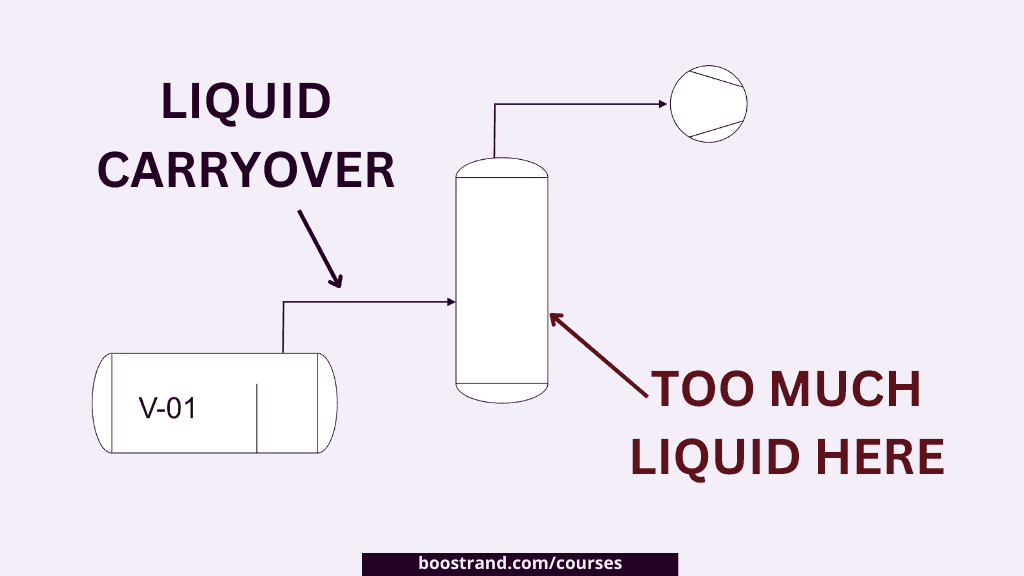
Troubleshooting
Operators started troubleshooting the issue. One of the measures that were followed in troubleshooting was to send a sample of the crude oil to the laboratory, and here came the issue. In the laboratory, a significant amount of asphaltenes and resins were discovered in addition to some workover fluids coming from well operations upstream of the separator.
The issue with these fluids is that they caused FOAMING inside the separator.
What is Foaming?
Foam is like tiny bubbles of gas covered with a thin layer of oil. This makes it harder for the gas and oil to separate efficiently. Foam shows up where the gas and oil meet when the pressure in the separator drops or because of things like surface tension, thickness of the liquid, and impurities in the oil. When this happens, small droplets are formed, and they get coated with oil. It occurs when the gas is released.
Usually, fast movement inside the separator causes foaming. The foam covers the liquid’s surface, making it tough for the gas to get out. Foam also takes up space in the separator for the gas and can get through the demister, escaping as a mix of mist and tiny liquid drops in the gas outlet.
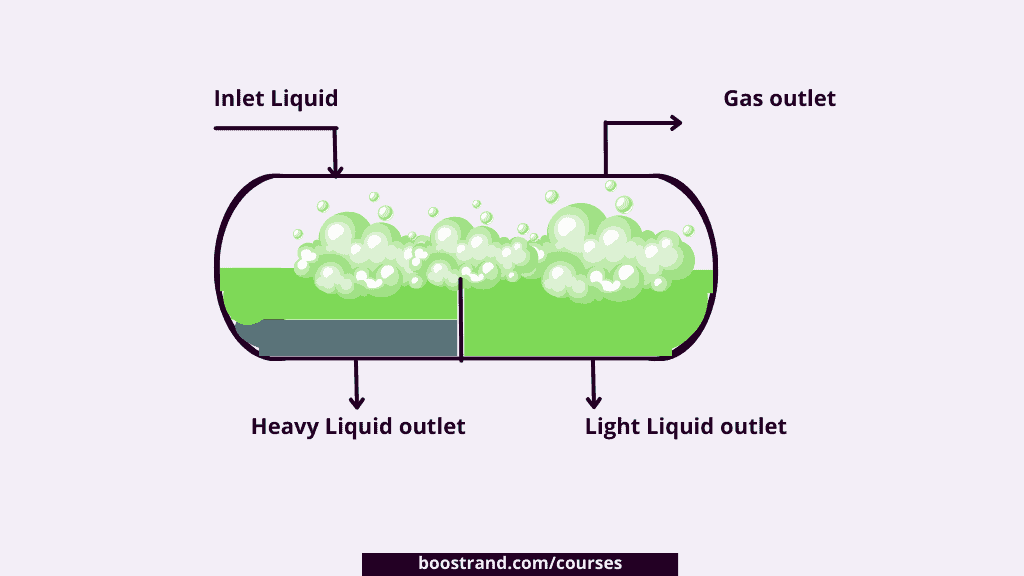
Issues Caused by Foaming
Foaming in a separator causes three main problems:
- Trouble Controlling Liquid Level: It’s harder to control how much liquid is in the separator because there are now three phases (liquid, gas, and foam) instead of the usual two.
- Foam Takes Up Space: Foam doesn’t weigh much but takes up a huge volume. This means it can fill up the separator, leaving less space for liquid to settle down. If the liquid level in the vessel was high, this shall cause liquid carryover in the outlet gas. If the liquid level in the vessel was low, gas carry-under will occur, which means that gas shall escape from liquid outlet.
- Removing Gas or Oil Gets Tricky: If foam is not controlled, it’s tough to get rid of separated gas or oil from the separator without bringing some foam along. This means that now the 3 phase separator is not functioning well as the outlet oil or gas specification is not as it should be.
Start your Career
Access Process Engineering Introduction Course
Available Solutions
So what shall the team do? The foaming issue was sent to the engineering team to start working on it.
In order to solve the issue and restore the separator to function well, there are 2 solutions:
- Short-term Solution: The fast solution is to inject antifoam depressants. This can help reduce the foam for the time being. But may lead to a great operating cost if much antifoam is needed.
- Long-term Solution: The more robust solution is to change the design of the separator. This can be through adding special internals at the inlet and outlet of the separator that catch foam, or it can be even by ordering a larger separator. This solution may end the issue of foaming. However, this solution will be very costly and needs much time to implement.
Way Forward
So which solution shall the team follow?
Short-Term Solution
It’s highly important to solve the issue on the short term as isolating the separator would lead to a total plant shutdown. This leads to a loss in plant production which means huge losses as long as the plant is not running.
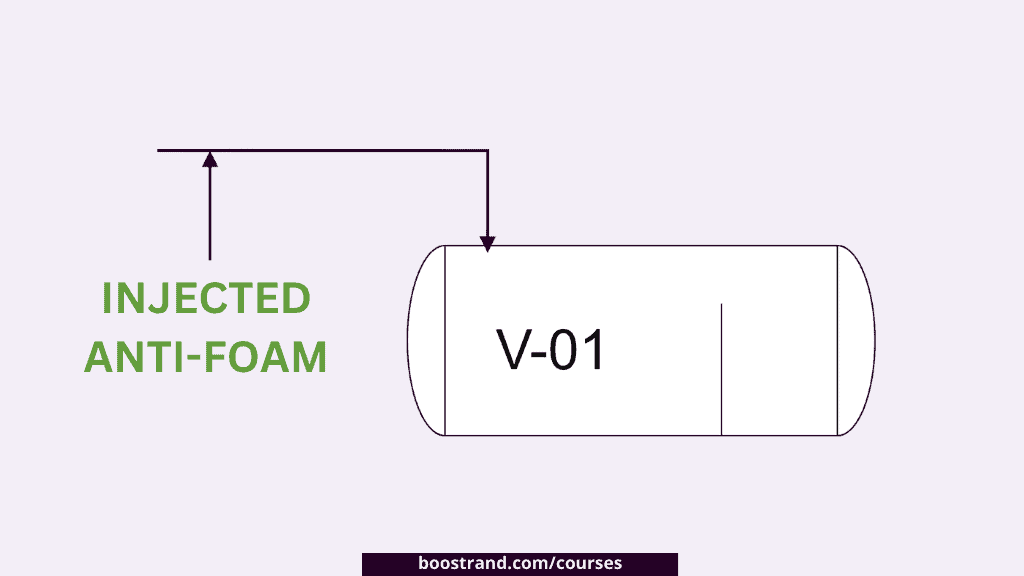
So here the separator should be restored to work efficiently as soon as possible. That’s why ANTI-FOAM injection is applied.
Over the following weeks, the team fine-tuned the dosage and injection points of the antifoam agent to optimize its effectiveness while managing operational costs.
Now, it was noticed that the level control in the separator was more stable. In addition, the liquid throughput to the compressor suction scrubber was significantly reduced, illustrating the efficacy of the antifoam treatment.
Long-Term Solution
So the introduction of antifoam injection solved the foaming issue to a great extent. However, it costed a lot. This is a continuous daily burden having a rental injection system in addition to the cost of the anti-foam itself. That’s why the engineering team was seeking to solve the foaming issue on the long term.
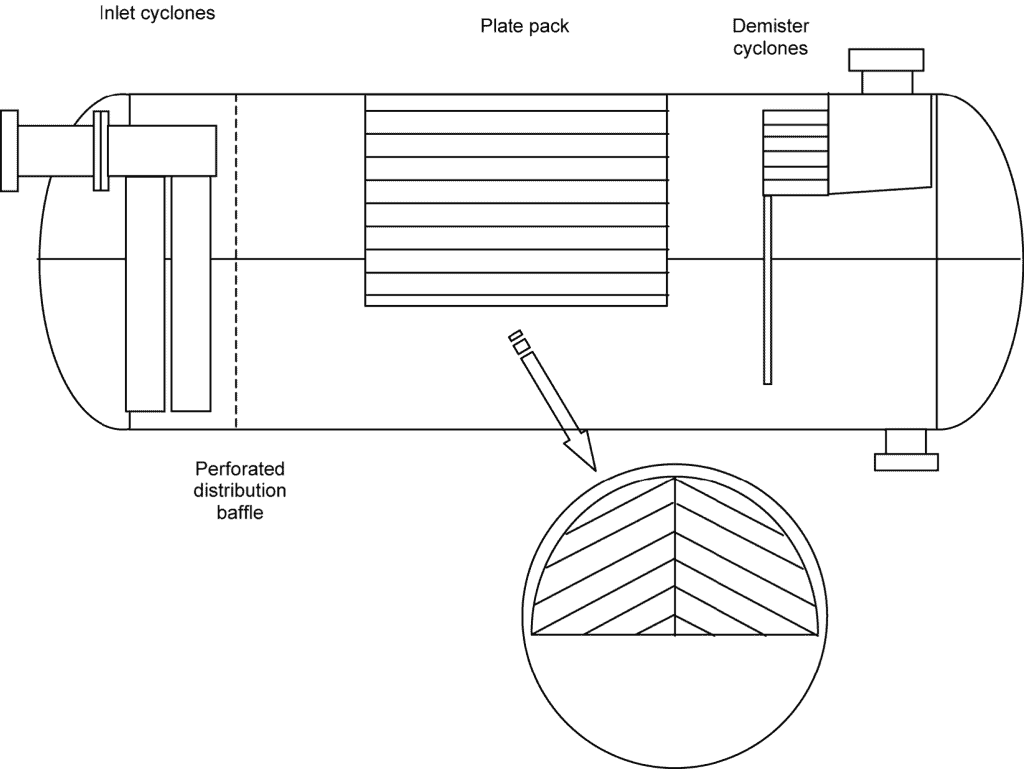
That’s why the engineering team started contacting a vessel internals separator vendor in order to suggest the internals needed.
The internals supplier suggested a retrofit plan that included the installation of a new inlet device and foam-breaking plates.
These internals were delivered and planned to be installed during the upcoming scheduled maintenance shutdown. There were great challenges related to welding these internals in the vessel as they can affect its mechanical integrity. However, these were taken into consideration during the assessment phase made by the internals supplier.
Finally, the internals were installed successfully and the vessel was R stamped during the maintenance shutdown period and it is now ready for start-up.
Now, after the start-up, the separator was functioning well without the need for anti-foam injection thanks to the new internals.
Conclusion
So we have seen how the change in composition of oil impurities negatively affected the separation efficiency and the operation of the whole plant. We have seen how the short-term anti-foam solution and long-term solution to add vessel internals were introduced to solve the foaming problem without causing prolonged plant shutdown and minimizing the cost as much as possible.
Disclaimer:
This case study is for instructional purposes only and represents a specific instance of addressing a process issue. The solutions provided are not universally applicable and should be considered as a potential approach rather than a definitive remedy. Readers should exercise their own judgment and consult with professionals when applying such strategies to their unique operational contexts.
Start your Career
Access Process Engineering Introduction Course
Share this:
[…] creation of a PFD is typically based on the output of process simulation software. We have discussed plant simulation’s role in a project in the previous article. In a nutshell, process simulation involves using specialized software to model and analyze the […]