In the world of engineering and project management, process design is a critical component of turning ideas and concepts into reality. Whether it’s a new chemical plant, an oil refining or gas, or petrochemical plant, or a power generation system, the process design stages play a crucial role in ensuring that the final product is efficient, safe, and reliable. In this article, we’ll take a deep dive into the various stages of process design, from the initial conceptual design to the final startup of the plant.
As we progress through each stage, we’ll explore the importance of each step, the key deliverables, the cost accuracy, the effect of change on the project, and the role of various engineering disciplines in shaping the final design. When the project team has the correct understanding of each stage within the project, this shall help give the optimum solutions that shall reduce overall project cost and avoid delay in the project.
Start your Career
Access Process Engineering Introduction Course
Importance of Process Design in Project Execution
Process design is a central element of any engineering project. It is the blueprint that guides the construction, operation, and maintenance of a facility. A well-executed process design ensures that the plant operates efficiently, safely, and in compliance with environmental regulations. It also helps to minimize capital and operating costs, making the project more financially viable. Ultimately, the success of any engineering project hinges on the quality and completeness of its process design.
So in the beginning, the process engineer creates the Process Flow Diagram (PFD) and Heat and Material Balance (HMB) summary, which determine the expected flow rate and physical properties of the fluid, fluid composition, operating pressure and temperature, and plant control.
Based on this information, downstream activities can be initiated, such as pipe and equipment sizing, hydraulic activities, equipment and line lists, P&ID, control system logic, equipment protection and shutdown logic, utility and effluent summary, PSV sizing and flare system requirements, and instrument specification process data. This article explains the main activities of process design and what a process engineer typically does in a project.
A process design shall give the information needed for our piping, instrumentation, and mechanical colleagues to proceed in their detailed activities, such as:
- Plant Layout
- 3D model and pipe isometrics creation based on the P&ID
- Purchase of equipment based on our sizing
- Purchase of different instruments based on the process data in hand
- Purchase of bulk items such as piping, valves, and fittings
- Consider the expected electrical loads needed by our plant
- And even more other activities…
All the above shall be based on process design requirements. As we see, The process design serves as a roadmap for the entire project team, from process engineers to construction managers and operators.
Start your Career
Access Process Engineering Introduction Course
Understanding the Project Phases is Highly Important
By following a systematic approach to design, the team can identify and address potential issues early on, reducing the risk of costly errors and delays during construction and startup. That’s why it should be understood that the maturity of process design depends on the project stage.
For example, in the very early project stages, process design is still very preliminary; that’s why it is not common to proceed with detailed activities or purchasing activities, as the design can change.
However, after the process design has reached a mature stage, where equipment, bulk material, and instruments are already purchased or even got constructed, it would be very difficult to change the design as it shall lead to a huge cost impact and project delay.
So let’s shed light on the main project stages:

Conceptual design: the foundation of process design
The first step in any process design journey is the conceptual design stage, which serves as the foundation for the entire project. It involves transforming the project’s initial idea into a preliminary design that outlines the basic process flow and identifies the major equipment required to achieve the desired outcome. Here are some key aims and common deliverables of the conceptual design stage:
Aims
- Define process requirements such as production capacity, product specifications, and environmental constraints through process simulation
- Conduct a preliminary feasibility assessment
- Establish a starting point for the subsequent design stages
- Provide a basis for decision-making and whether we shall proceed in this project or not
Common deliverables
- Process simulation
- Process flow diagram (PFD)
- Preliminary equipment list
- Initial cost estimate
Cost Accuracy
± 30- 50% of the estimated budget
Flexibility to Modifications
High
The resulting deliverables from a conceptual design provide a solid starting point for the subsequent design stages, allowing for a more efficient and effective process design journey. By emphasizing the importance of conceptual design, the project team can establish a strong foundation that sets the stage for success.
Start your Career
Access Process Engineering Introduction Course
Basic engineering / FEED : laying the groundwork for detailed design
Following the conceptual design, the project moves into the Front-End Engineering Design (FEED) stage. The FEED stage is a crucial step in the process design journey, as it bridges the gap between the preliminary concept and the detailed design that follows. During this stage, the process design is refined and expanded upon, with a focus on optimizing the process flow, equipment selection, and overall plant layout.
Aims
- Develop a comprehensive plan for the project
- Ensure process flow is efficient and optimized
- Identify and assess risks
- Lay the foundation for the subsequent detailed engineering stage
Common deliverables
- Process flow diagram (PFD) with a high accuracy
- Preliminary P&ID
- More accurate equipment list
- Equipment and instrument datasheets
- More accurate cost estimate
These documents serve as the basis for the detailed engineering stage, where the focus shifts to the final design and specification of all equipment, piping, and instrumentation.
Cost Accuracy
± 10- 30% than the estimated budget
Flexibility to Modifications
Still high flexibility. But less than the conceptual design
Overall, the FEED and basic engineering stages lay the foundation for a successful project outcome. The careful planning, analysis, and documentation produced during these stages ensure that the project moves forward with a clear understanding of its goals and constraints, reducing the risk of delays, cost overruns, and technical problems down the line.
Start your Career
Access Process Engineering Introduction Course
Detailed engineering: finalizing equipment and pipe sizing, hydraulics, and plant 3D model
The detailed engineering stage is a critical phase in the process design journey, where the final design and specification of all equipment, piping, and instrumentation are completed. The aim of this stage is to finalize equipment and pipe sizing, and hydraulics and develop a comprehensive 3D model of the plant.
Detailed design in itself passes through different stages.
For example, in its beginning, we haven’t purchased anything yet. We don’t have enough vendor data, so there is still some room for changes.
Then afterward, HAZOP and SIL sessions are conducted to challenge the design and ensure that the system is well protected; some changes may arise here due to the HAZOP outcome. In our P&ID course, we have gave examples on how HAZOP and SIL are applied on a P&ID design.
We shall then start to receive the data from vendors and incorporate it into our design. Here, we have already purchased the material we need. So changes shall be very limited and, in many cases, not tolerated.
Here are some key aims and common deliverables of the detailed engineering stage:
Aims
- Finalize sizing equipment and pipe in addition to hydraulic checks
- Incorporate the final data from vendors
- Develop a comprehensive 3D model of the plant
- Ensure that the final design meets all technical, safety, and regulatory requirements
Common deliverables
- Final Piping and Instrumentation Diagram (P&ID)
- Final equipment and instrument data are now verified by their vendors
- Piping isometrics
- Completed 3D model
- Detailed construction schedule
Cost Accuracy
±0- 10% than the estimated budget, depending on which phase we are in.
Flexibility to Modifications
Low flexibility. Any change can affect the project cost and cause delays to the project.
Start your Career
Access Process Engineering Introduction Course
The detailed engineering stage requires close collaboration among the project team, equipment vendors, construction contractors, and other stakeholders to ensure that the final design meets all technical, safety, and regulatory requirements. The resulting deliverables serve as the basis for the procurement, construction, and commissioning of the plant.
With a focus on finalizing equipment and pipe sizing, hydraulics, and developing a comprehensive 3D model of the plant, the detailed engineering stage sets the stage for a successful construction and startup process.
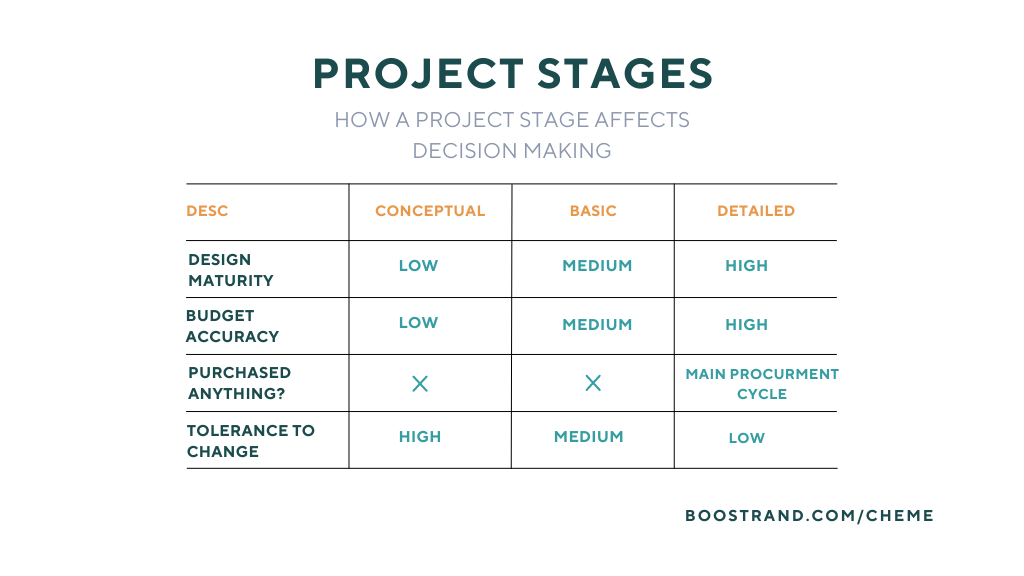
Commissioning and startup: bringing the process to life
Once the process design has been completed and the plant has been constructed, the final stage is the commissioning and startup of the facility. This is where the process design comes to life, as the plant is brought online and begins to produce the desired products.
Commissioning and startup form a critical phase of the project that includes:
- Ensuring that the plant was constructed as per the design
- Verification of control schemes
- Carry out leak tests to prepare for start-up
- Any issues that arise during startup are addressed and resolved, and the plant is gradually ramped up to full production capacity.
- Fine-tuning of operating parameters to ensure that the plant meets its performance targets
- Performance testing of all equipment
Once the plant has achieved steady-state operation, the final step is to hand over the facility to the operations team. This includes the transfer of all documentation, such as equipment manuals, maintenance procedures, and operating instructions, as well as the training of personnel on the safe and efficient operation of the plant.
Conclusion: the importance of a well-executed process design
In conclusion, the process design stages play a crucial role in the successful execution of any engineering project. From the initial conceptual design to the final commissioning and startup, each stage serves a specific purpose in turning ideas and concepts into a functioning plant.
The importance of a well-executed process design cannot be overstated. It ensures that the plant operates efficiently, safely, and in compliance with environmental regulations. It helps to minimize capital and operating costs, making the project more financially viable. And it lays the foundation for the long-term success of the facility, ensuring that it meets the needs of its stakeholders for years to come.
By understanding the intricacies of each process design stage, engineers and project managers can appreciate the complexity and importance of the overall process design. They can identify potential issues early on, reducing the risk of costly errors and delays during construction and startup. And they can work together to ensure that the final plant is safe, reliable, and capable of meeting its performance targets.
So, the next time you’re involved in an engineering project, remember the critical role that process design plays in its success. By focusing on each stage of the process design journey, you can help to ensure that your project is completed on time, within budget, and to the highest standards of quality and safety.
Start your Career
Access Process Engineering Introduction Course
Share this:
[…] creation of a PFD is typically based on the output of process simulation software. We have discussed plant simulation’s role in a project in the previous article. In a nutshell, process simulation involves using specialized software to model and analyze the […]